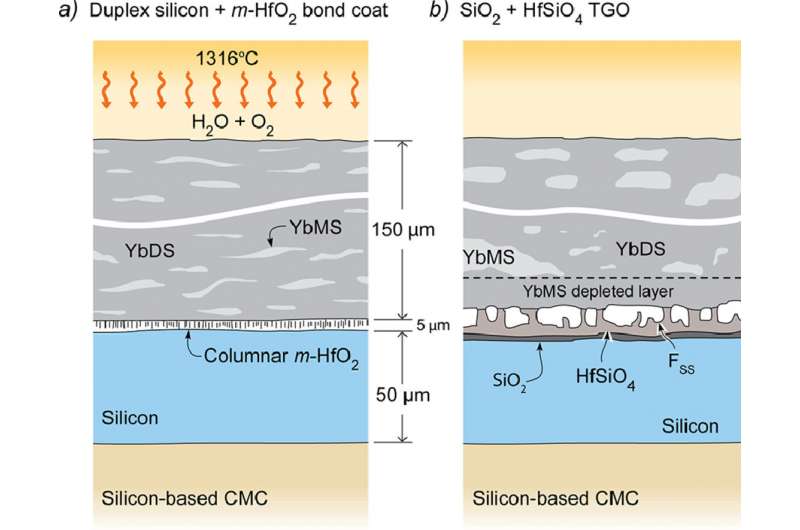
Post-pandemic vacation travel was among the biggest stories of summer
2021, raising questions about air travel's contribution to greenhouse
gas emissions and climate change. According to the Environmental and
Energy Study Institute, 710 million tons of global carbon dioxide came
from commercial aviation in 2013. By 2017, that number reached 860
million tons, a 21% increase in four years. By 2018, it climbed to 905
million tons, 2.4% of total CO2 emissions.
Airplane manufacturers and their customers in government and industry have invested in the design of new aircraft engines that function at extremely high temperatures, which means the engines can generate more energy while burning less fuel. However, the very high temperatures can be a problem for the materials used to make the engine.
Haydn Wadley, Edgar Starke Professor of Materials Science and Engineering at the University of Virginia School of Engineering and Applied Science, and Jeroen Deijkers, a postdoctoral research associate in Wadley's group, found a way to greatly extend the life of the materials used in these jet engines. Their paper, "A duplex bond coat approach to environmental barrier coating systems," is published in the September 2021 issue of Acta Materialia.
"A jet engine gulps huge quantities of air, which, when compressed and mixed with hydrocarbon fuel and burned in a combustor, powers the plane's propulsion system. The hotter the combustor, the more efficient the engine," Wadley said.
Combustion in airplane engines now reaches or exceeds 1500 degrees centigrade, well above the melting temperatures of engine parts typically made of nickel and cobalt alloys. Research has turned to ceramics that can withstand these temperatures, but they must contend with chemical reactions from the water vapor and unburnt oxygen in the extreme combustion environment.
Silicon carbide is the ceramic of choice. However, engine parts made of silicon carbide would last only a few thousand hours of flight time. At such high temperatures, the carbon element reacts with oxygen to form carbon monoxide (a gas), while the silicon forms silica (a solid), but silica reacts with water vapor to form a gaseous silicon hydroxide. In other words, the engine part progressively turns into gas and disappears out the tail pipe.
To protect the ceramic parts, engine manufacturers apply a two-layer coating, called an environmental barrier coating system, to the silicon carbide. The outer layer is designed to slow the spread of oxygen and water vapor toward the silicon carbide during flight, while an inner bond coat made of silicon protects the silicon carbide's surface by reacting with the oxygen to form a thin layer of silica. But there are still challenges to this design.
"The life of the engine component is often dictated by the time it takes for the silica layer thickness to reach a critical point where the stress caused by expansion and contraction during repeated heating and cooling causes the coating to pop off," Wadley said.
Scientists and engineers have two basic strategies to delay the coating's separation and extend the life of expensive engine components. They can make the outer coating layer very thick to slow down the arrival of oxygen at the bond coat, but that adds weight and cost. Or, they can create a different kind of protective oxide, one that does not "pop off."
Deijkers and Wadley pursued the second strategy.
Their solution uses an outer layer of ytterbium disilicate, a rare earth element that shares silicon's and silicon carbide's thermal expansion characteristics and is slow to transport oxygen and water vapor toward the silicon layer. They first deposited the silicon bond coat and then placed a thin layer of hafnium oxide between the silicon and the ytterbium disilicate outer layer.
Their experimental studies show that as the silica forms on the silicon, it immediately reacts with the hafnia to form a silicon-hafnium oxide, or hafnon. The hafnon's thermal expansion and contraction is the same as the rest of the coating and will never cause the coating to pop off or crack. Wadley calls it adding a little "hafnia fairy dust."
"When we deposit a very thin layer of hafnia on top of silicon, followed by a layer of ytterbium disilicate, the oxygen that passes through the ytterbium disilicate creates a chemical reaction with the underlying materials to form the hafnon," Deijkers said.
Deijkers' access to unique equipment in Wadley's lab, specifically a directed vapor deposition system, enabled this breakthrough in environmental barrier coatings. The ability to deposit a film of ytterbium disilicate that is thinner than the diameter of a human hair is key to their success.
The directed vapor deposition process uses a powerful 10-kilowatt focused electron beam to melt material in a low-pressure chamber. A supersonic gas jet transports the vapor to the silicon-coated silicon carbide where it condenses, creating a thin film. They then use a plasma spray method to deposit the final ytterbium disilicate layer, and the coated component is then ready for testing.
Deijkers successfully defended his dissertation in October 2020, combining his interests in aircraft and high-temperature materials for his Ph.D. research, and following his father's path into materials science and engineering.
"My dad used to work on dredging ships. Seeing the pump house glowing orange-white in the furnace, that's how I caught the engineering bug," Deijkers said.
Deijkers, who is from the Netherlands, combined these early memories with his interest in serving in the Dutch Air Force, earning a bachelor's and master's degree in aerospace engineering from Delft University of Technology.
When Deijkers began applying to Ph.D. programs in the United States, his master's thesis on thermal barrier coatings captured Wadley's attention. Deijkers' arrival was well timed. Group member Brad Richards, who earned his Ph.D. in materials science and engineering from UVA in 2015, had developed the silicon-ytterbium disilicate coating system for ceramics that was subsequently found to be very similar to that being used by the makers of aircraft engines.
Deijkers' dissertation improves Richards' coating system, deepening understanding of the surface chemistry involved and increasing the coating system's viability for commercial adoption.
"One set of questions driving my research focused on how long it takes for the hafnon to form through the oxidation process," Deijkers said. "I wanted to understand how this process really works, and whether we could actually put it to use.
"This coating has greater potential than we thought; we need to develop it and put it in an actual engine, to move it further along the path toward commercialization."
Today's methods are rooted in deposition techniques developed in the 1970s.
"Compared to the state-of-the-art in industry, our research makes a major improvement," Deijkers said. "My rough estimate, if industrial manufacturers were able to implement these newer processing techniques, they could extend the engine parts' lifetime by as much as 200 times. But there are a lot of hurdles to jump through to get that level of performance."
Wadley's research group made these advancements with the support of the Office of Naval Research, which awarded Wadley's team two successive grants over a period of six years.
"The problems we have to solve are multi-disciplinary and multi-institutional," Wadley said. "We need to fuse together knowledge from mechanics, chemistry and materials science in order to make progress. Beyond the immediate need to reduce CO2 emitted by propulsion technology, our research supports the global shift from carbon-containing hydrocarbons to hydrogen fuels and the eventual electrification of air travel platforms."
Whereas Deijkers hopes to attract private industry to the team's coatings system and deposition process, his career ambition is to pursue scientific discoveries at a national laboratory or in academia.
"The nation has an urgent need for talent in this arena," Wadley said. "We are in desperate need for bright, creative people who want to be trained to solve these kinds of problems for society going forward."
Just as Deijkers continued Richards' research, he encourages UVA Engineering undergraduates to participate in the interdisciplinary research underway in Wadley's group.
"We had undergraduates from aerospace engineering, physics, systems
engineering," Deijkers said. "We are working a lot of different aspects
of the problem—computer modeling, materials synthesis, thermo-mechanical
life design. We always have things for undergraduates to do, and we're
always open for them to do research with us."