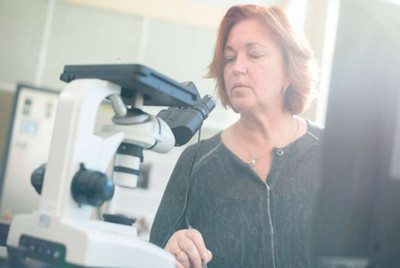
Manufacturing products from titanium and its alloys using traditional methods remains a complex technological task that requires a lot of time and money. Scientists at South Ural State University have developed a new universal technology for manufacturing titanium alloy parts using additive technologies. The new technology will allow significant savings in further machining. An article about the study was published in Materials.
Titanium is widely used in mechanical engineering and aviation due to its strength. However, to a greater extent, traditional foundry production is used for the manufacture of these parts. The use of additive technologies seems to represent a very promising direction since it can produce products of complex geometric shapes from titanium and its alloys with relatively little subsequent machining.
"The production of parts by casting is a very complex technological process. It must be produced in a controlled atmosphere (under vacuum or in a protective gas environment) to avoid the interaction of the titanium melt with oxygen and nitrogen in the air. And further machining of such parts requires certain conditions and equipment; therefore, it is notable for its high cost. The use of additive technologies seems to be a very promising direction, since it can allow creating products of complex geometric shapes from titanium and its alloys with little machining. This will significantly reduce the price of the finished product," explains SUSU Professor Marina Samodurova, doctor of technical sciences.
The aim of the work of scientists of South Ural State University together with specialists of Composite JSC was to develop a technology for manufacturing parts from titanium alloys employing a combination of two additive manufacturing technologies: selective laser melting (SLM) and direct metal deposition (DMD) processes. The work of SUSU was to develop a technology for producing structural elements from powdered titanium alloys implementing the DMD method on blanks made using SLS processes.
As part of the work of the International Laboratory of Mechanics, Laser Processes and Digital Production Technologies, SUSU conducted a study of the structure and micro-hardness of manufactured parts made of titanium alloys using high-precision laboratory equipment.
"The analysis of the chemical composition of various parts made by laser surfacing, the analysis of the uniformity of the chemical composition in the height of the product, as well as the composition of individual structural components was carried out. All the samples examined have a microstructure characteristic of the hardened state of two-phase titanium alloys, which means they have the necessary strength and hardness that is required from such products," says Marina Samodurova.
During the experiment, a technological decision was made about the external thermal protection of the process chamber. This minor upgrade of the standard FL-Clad-R-4 laser-surfacing system prevented cracking of the obtained parts after cooling. The scientists obtained products with good performance in terms of strength characteristics. The results of the experiment showed that parts made of titanium and titanium alloys obtained using additive technologies can be successfully used in mechanical engineering and aviation, as they have excellent reliability and a large margin of safety.