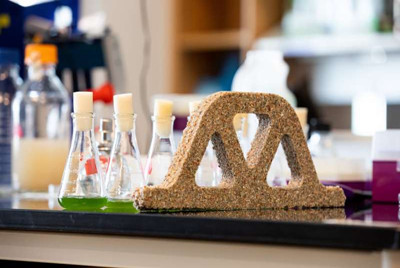
University of Colorado Boulder researchers have developed a new approach to designing more sustainable buildings with help from some of the tiniest contractors out there.
In a study that will appear Jan. 15 in the journal Matter, engineer Wil Srubar and his colleagues describe their strategy for using bacteria to develop building materials that live and multiply—and might deliver a lower carbon footprint, to boot.
"We already use biological materials in our buildings, like wood, but those materials are no longer alive" said Srubar, an assistant professor in the Department of Civil, Environmental and Architectural Engineering (CEAE). "We're asking: Why can't we keep them alive and have that biology do something beneficial, too?"
You can't buy these microorganisms turned bricks at your local Home Depot just yet. But the researchers say that their ability to keep their bacteria alive with a high success rate shows that living buildings might not be too far off in the future.
Such structures could, one day, heal their own cracks, suck up dangerous toxins from the air or even glow on command.
"The sky's the limit for our creativity," Srubar said.
The same might not be true for today's more corpse-like building materials, which he said can be costly and polluting to manufacture: Making the cement and concrete alone needed for roads, bridges, skyscrapers and other structures generates nearly 6% of the world's annual emissions of carbon dioxide.
Srubar's solution: Hire some bacteria.
In particular, he and his colleagues experimented with cyanobacteria belonging to the genus Synechococcus. Under the right conditions, these green microbes absorb carbon dioxide gas to help them grow and make calcium carbonate—the main ingredient in limestone and, it turns out, cement.
To begin the manufacturing process, the researchers inoculate colonies of cyanobacteria into a solution of sand and gelatin. With the right tweaks, the calcium carbonate churned out by the microbes mineralize the gelatin which binds together the sand—and, presto, a brick.
"It's a lot like making rice crispy treats where you toughen the marshmallow by adding little bits of hard particles," Srubar said.
As an added bonus, such bricks would actually remove carbon dioxide from the air, not pump it back out.
They're durable, too. In the new study, the team discovered that under a range of humidity conditions, they have about the same strength as the mortar used by contractors today.
"You can step on it, and it won't break," he said.
The researchers also discovered that they could make their material reproduce. Chop one of these bricks in half, and each of half is capable of growing into a new brick.
Those new bricks are resilient: According to the group's calculations, roughly 9-14% of the bacterial colonies in their materials were still alive after 30 days and three different generations in brick form. Bacteria added to concrete to develop self-healing materials, in contrast, tend to have survival rates of less than 1%.
"We know that bacteria grow at an exponential rate," Srubar said. "That's different than how we, say, 3-D-print a block or cast a brick. If we can grow our materials biologically, then we can manufacture at an exponential scale."
He notes that there's a lot of work to do before that happens. The team's cyanobacteria, for example, need humid conditions to survive—something that's not possible in more arid regions of the world. So he and his team are working to engineer microbes that are more resistant to drying out so they remain alive and functional.
But the possibilities are big. Srubar imagines a future in which suppliers could mail out sacks filled with the desiccated ingredients for making living building materials. Just add water, and people on site could begin to grow and shape their own microbial homes.
"Nature has figured out how to do a lot of things in a clever and efficient way," Srubar said. "We just need to pay more attention."