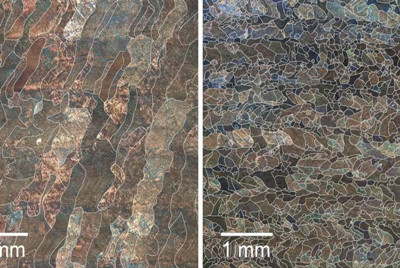
Researchers have used sound vibrations to shake metal alloy grains into tighter formation during 3-D printing.
A study just published in Nature Communications shows high frequency sound waves can have a significant impact on the inner micro-structure of 3-D printed alloys, making them more consistent and stronger than those printed conventionally.
Lead author and Ph.D. candidate from RMIT University's School of Engineering, Carmelo Todaro, said the promising results could inspire new forms of additive manufacturing.
"If you look at the microscopic structure of 3-D printed alloys, they're often made up of large and elongated crystals," Todaro explained.
"This can make them less acceptable for engineering applications due to their lower mechanical performance and increased tendency to crack during printing."
"But the microscopic structure of the alloys we applied ultrasound to during printing looked markedly different: the alloy crystals were very fine and fully equiaxed, meaning they had formed equally in all directions throughout the entire printed metal part."
Testing showed these parts had a 12% improvement in tensile strength and yield stress compared with those made through conventional additive manufacturing.
The team demonstrated their ultrasound approach using two major commercial grade alloys: a titanium alloy commonly used for aircraft parts and biomechanical implants, known as Ti-6Al-4V, and a nickel-based superalloy often used in marine and petroleum industries called Inconel 625.
By simply switching the ultrasound generator on and off during printing, the team also showed how specific parts of a 3-D printed object can be made with different microscopic structures and compositions, useful for what's known as functional grading.
Study co-author and project supervisor, RMIT's Distinguished Professor Ma Qian, said he hoped their promising results would spark interest in specially designed ultrasound devices for metal 3-D printing.
"Although we used a titanium alloy and a nickel-based superalloy, we expect that the method can be applicable to other commercial metals, such as stainless steels, aluminium alloys and cobalt alloys," Qian said.
"We anticipate this technique can be scaled up to enable 3-D printing of most industrially relevant metal alloys for higher performance structural parts or structurally graded alloys."
The article 'Grain structure control during metal 3D printing by high-intensity ultrasound' is published in Nature Communications.