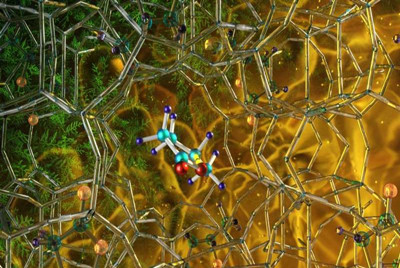
Researchers led by the University of Manchester have designed a catalyst that converts biomass into fuel sources with remarkably high efficiency and offers new possibilities for manufacturing advanced renewable materials.
Neutron scattering experiments at the Department of Energy's Oak Ridge National Laboratory played a key role in determining the chemical and behavioral dynamics of a zeolite catalyst—zeolite is a common porous material used in commercial catalysis—to provide information for maximizing its performance.
The optimized catalyst, called NbAlS-1, converts biomass-derived raw materials into light olefins—a class of petrochemicals such as ethene, propene, and butene, used to make plastics and liquid fuels. The new catalyst has an impressive yield of more than 99% but requires significantly less energy compared to its predecessors. The team's research is published in the journalNature Materials.
"Industry relies heavily on the use of light olefins from crude oil, but their production can have negative impacts on the environment," said lead author Longfei Lin at the University of Manchester. "Previous catalysts that produced butene from purified oxygenated compounds required lots of energy, or extremely high temperatures. This new catalyst directly converts raw oxygenated compounds using much milder conditions and with significantly less energy and is more environmentally friendly."
Biomass is organic matter that can be converted and used for fuel and feedstock. It is commonly derived from leftover agricultural waste such as wood, grass, and straw that gets broken down and fed into a catalyst that converts it to butene—an energy-rich gas used by the chemical and petroleum industries to make plastics, polymers and liquid fuels that are otherwise produced from oil.
Typically, a chemical reaction requires a tremendous amount of energy to break the strong bonds formed from elements such as carbon, oxygen, and hydrogen. Some bonds might require heating them to 1,000°C (more than 1,800°F) and hotter before the bonds are broken.
For a greener design, the team doped the catalyst by replacing the zeolite's silicon atoms with niobium and aluminum. The substitution creates a chemically unbalanced state that promotes bond separation and radically reduces the need for high degrees of heat treatments.
"The chemistry that takes place on the surface of a catalyst can be extremely complicated. If you're not careful in controlling things like pressure, temperature, and concentration, you'll end up making very little butene," said ORNL researcher Yongqiang Cheng. "To obtain a high yield, you have to optimize the process, and to optimize the process you have to understand how the process works."
Neutrons are well suited to study chemical reactions of this type due to their deeply penetrating properties and their acute sensitivity to light elements such as hydrogen. The VISION spectrometer at ORNL's Spallation Neutron Source enabled the researchers to determine precisely which chemical bonds were present and how they were behaving based on the bonds' vibrational signatures. That information allowed them to reconstruct the chemical sequence needed to optimize the catalyst's performance.
"There's a lot of trial and error associated with designing such a high-performance catalyst such as the one we've developed," said corresponding author Sihai Yang at University of Manchester. "The more we understand how catalysts work, the more we can guide the design process of next-generation materials."
Synchrotron X-ray diffraction measurements at the UK's Diamond Light Source were used to determine the catalyst's atomic structure and complementary neutron scattering measurements were made at the Rutherford Appleton Laboratory's ISIS Neutron and Muon Source.
In addition to Lin, Cheng, and Yang, the list of coauthors includes Alena M. Sheveleva, Ivan da Silva, Christopher M. A. Parlett, Zhimou Tang, Yueming Liu, Mengtian Fan, Xue Han, Joseph H. Carter, Floriana Tuna, Eric J. L. McInnes, Luke L. Daemen, Svemir Rudi?, Anibal J. Ramirez-Cuesta, and Chiu C. Tang.