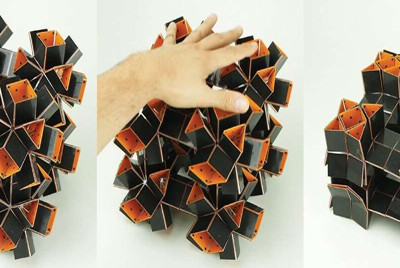
AMOLF researchers are studying three-dimensional prismatic structures that can assume different shapes with the aim of producing metamaterials that have multiple properties. Researchers have found a new way to simulate the deformations in such structures, and in doing so, they discovered a wide range of unexpected shapes. The results will be published today in the scientific journal Nature Communications.
It is fundamental mathematical research but also very tangible. On the desk lies a complex, origami-like construction made from plastic squares. However, when compressed, it folds up and forms a compact structure that is more similar to an apartment block with four towers. Which shapes the structure can assume is predicted by a new calculation method developed by AMOLF researchers Agustin Iniguez-Rabago, Yun li and Bas Overvelde from the Soft Robotic Matter group.
The structure is a model for a three-dimensional mechanical metamaterial, which was built by hand by Iniguez-Rabago. Additionally, the material is multistable, which means that it can retain several shapes without exerting force on it.
"You might still remember the so-called Slap Wrap bracelets that you could throw on your wrist and that were stable in both a straight and a round shape," says AMOLF group leader Overvelde. "The structures that we have investigated show similar behavior, but with far more possibilities." However, not all the materials that the researchers work with can be intuitively understood in this manner, says Iniguez-Rabago. "For some structures, we did not expect that they would demonstrate multistable behavior. I was amazed that this simply rolled out of our new computer algorithm."
Mini robots
Metamaterials have special properties that depend on their shape in addition to the material they are made of. There are many possible applications if researchers can gain a good understanding of how the shape determines the properties. These materials could then be used as mini-robots or systems to store energy, for example. "We have built structures at the centimeter scale to check whether our calculations are correct. However, the underlying mechanical behavior should also be applicable at far smaller or larger scales," Overvelde says.
Using their model, the researchers managed to calculate large quantities of three-dimensional models. Iniguez-Rabago says, "We want to know how many stable shapes a certain design has. Up until now, people often used a two-dimensional model and tried to describe that as precisely as possible. However, far more is possible with our new calculation method. We can now investigate three-dimensional metamaterials which exhibit highly complex behavior that is difficult to predict."
Flexible surfaces
The researchers made two important choices to realize the simulations. The first was by making the surfaces of the structures somewhat flexible. This allowed for an easier transition from one shape to another, which results in more stable shapes per structure. The second choice was not to allow the computer to randomly calculate all possible shapes, but only unique combinations of applied forces on the hinges. "In a certain sense, we pinch a structure in various ways and observe whether the structure jumps to another shape; it is very similar to how one would carry out experiments." This makes the calculations far simpler. "With this approach, we sometimes found over 100 stable shapes for one structure," says Iniguez-Rabago.
Controlled movement
The researchers verified their simulations by manufacturing the structures and performing experiments. Now, they will take it a step further. By slightly moving a single hinge (by inflating a single balloon in the model), they can drastically change the shape of the entire structure. "We can use this idea in later applications," Iniguez-Rabago explains. "With responsive materials such as hydrogels, we can build a structure on a far smaller scale and control how it moves. That is our ultimate goal."